Temarry Recycling provides efficiency in the management of recyclable hazardous and non-hazardous wastes that are compatible with our distillation and Waste to Energy systems. Liquids received are filtered and blended in one of our blending tanks and then directed to one of our solvent recovery stills. Solid waste received is thermally treated at 1500°F using the heat value to generate steam that operates our recovery stills. We receive liquids, solids, semi-solids and sludges for recycling. Material can be shipped in drums, cubic yard boxes/bags, totes and tankers.
Types of wastes that can be received are:
- Flammable solvents including alcohols
- Ketones
- Naphtha
- Paint related materials
- Flammable mixtures with and without halogens
Most organic solids with fuel value. Non RCRA waste including oils, oily water, antifreeze and latex paint.
Through a highly coordinated truck transportation network, Temarry Recycling provides reliable, cost-effective transportation for cradle to grave waste management. All waste is processed on site receiving an H020 handling code for distillation or an H050 handling code for, “energy recovery at this site”.
Solvent Recycling and Energy Recovery Process
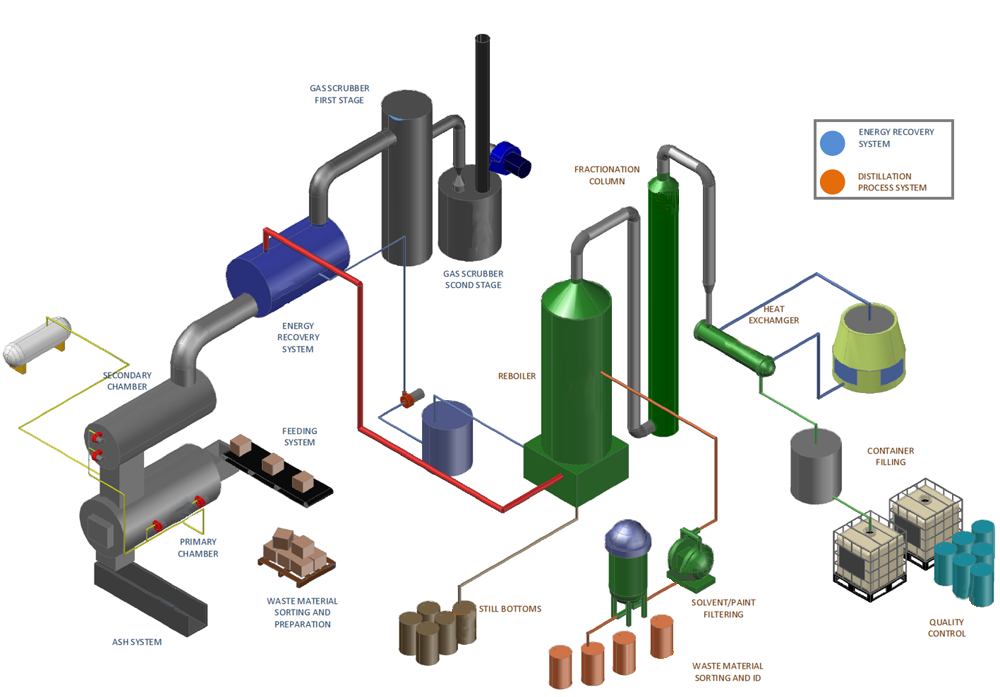
Waste solids are received, sorted and finger print analysis performed
Solids are packaged into proper size burnable containers and placed on the feed conveyor
Burn in the primary chamber is initiated by clean burning propane gas that heats the primary chamber to 1500 F, which is the basic operating temperature. Once at this operating temperature, the unit becomes self-sustaining and the primary burner turns off. Heat then travels to the secondary chamber.
Solids, or ash, fall out of the burn unit on to the ash conveyor system and deposited into an ash hopper. Ash is later blended with other liquids for cement kiln fuel blending.
All vapor from the primary burn chamber are directed to the secondary chamber where there is a retention time of 2.5 seconds. All volatile organic compounds are eliminated by thermal destruction.
Thermal energy is converted to steam in our 200 horse power boiler. Steam is directed to the distillation units for use as a heat source.
Additional heat from the boiler is directed to a two stage venturi scrubber system to insure that only clean water vapor is emitted to the atmosphere
Stage two of the two stage gas scrubber
Waste solvents are received, sorted and finger print analysis performed
Liquid drums are pumped and filtered
After filtering, solvents are pumped to the distillation unit
Volatilized solvent vapors expand into the fractionation column
Pure solvent is cooled down through a heat exchanger and is directed to a finished product tank
Product is packaged into drums and totes for distribution back in to industry